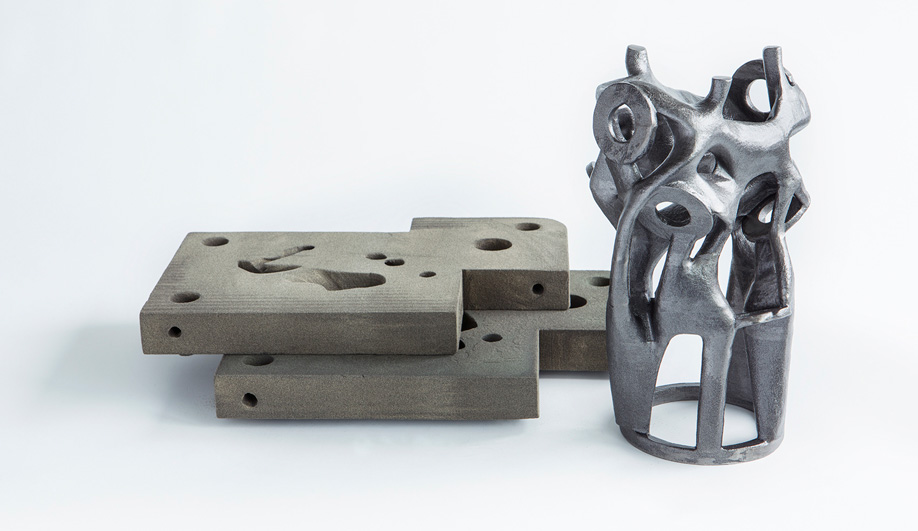
International design and engineering firm Arup finds a shortcut to casting complex steel nodes by using 3D printing technology.
Like many of her peers, Salomé Galjaard has spent the past few years investigating ways 3D printing can help create more efficient and diverse architectural forms. But while others are using the technology to form building components – and even entire structures – Galjaard is reconsidering digital fabrication’s role in the design process. In her latest research, the senior designer at international design and engineering firm Arup combines the newest 3D software with old-school manufacturing methods to economically produce complex structural parts on a bespoke level.
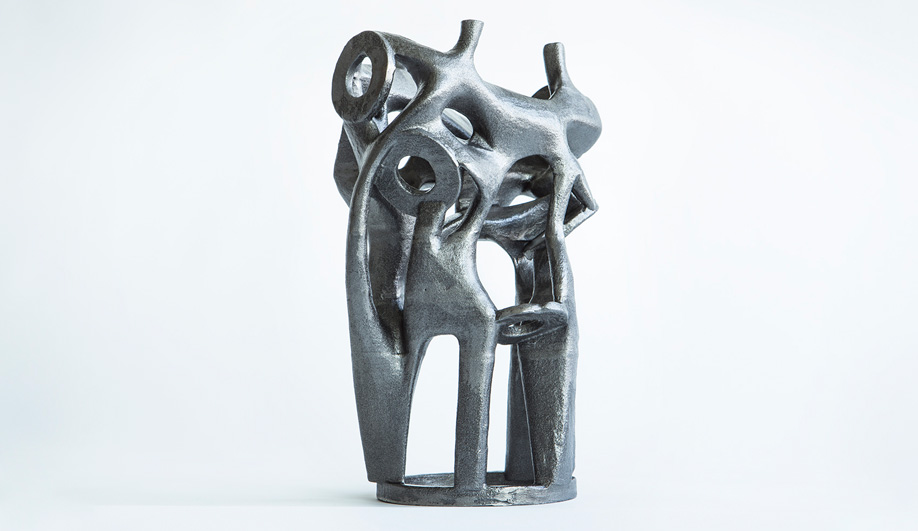
As part of Arup’s Amsterdam team, Galjaard was working on a tensegrity structure that is part of a lighting system for a shopping strip in The Hague. The structure required a series of unique metal nodes (such as the one shown above) that would be time-consuming and expensive to manufacture. Galjaard was familiar with the use of 3D-printed sand moulds for the casting of small, certified metal parts. Common in industrial and automotive design, the method turned out to be ideal for the iterative nature of developing and testing such components, since the moulds are simple to produce and easily adapted, and the filament can be reused.
Arup worked with specialists 3Dealise to create sand-printed moulds made using structural analysis software, including Optistruct, (to optimize the material layout) and Rhino 3D (for the modelling). “These printing technologies have been around for decades,” Galjaard says, “but combining them with increased computational power allows us to embrace project complexity in design and use these techniques to their best advantage – not to slightly improve a current solution, but to do something completely different.”
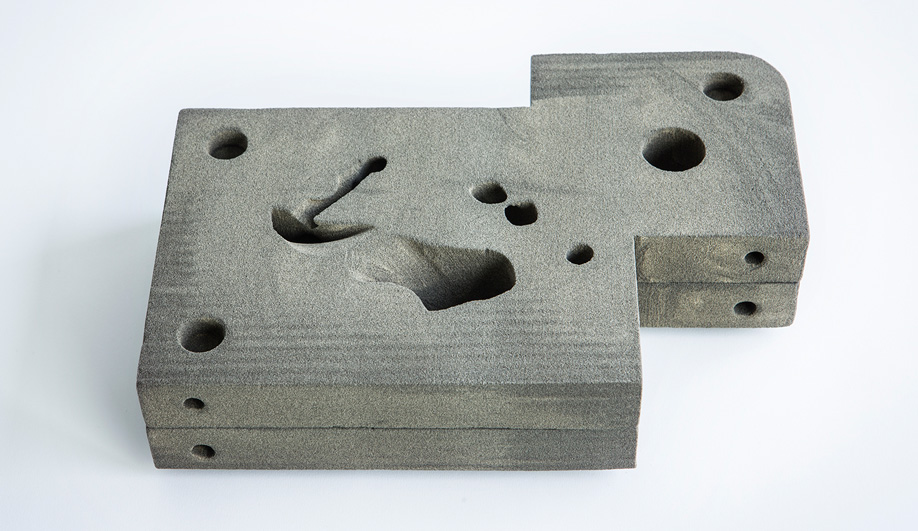
The moulds allow certified metal nodes to be formed at a lower cost, and in less time than if they were directly printed. The final products have the same structural integrity as traditional welded parts but are smaller and up to 75 per cent lighter.
Galjaard predicts that this project will inform further research. “It would be interesting to consider the use of fibre-reinforced materials and how to process them to find more structural applications in the building sector. Hybrid technologies massively increase the range of options.” Galjaard also hopes to collaborate with builders to understand how this process can be used in the future on a larger scale.
Why print a mould instead of a metal part?
- Sand moulds are inexpensive, easily adapted and recyclable
- Certified metal nodes can be made in small numbers, at a lower cost
- A more complex module is formed in less time
- The final product is smaller and lighter
This story was taken from the March/April 2018 issue of Azure. Buy a copy of the issue here, or subscribe here.