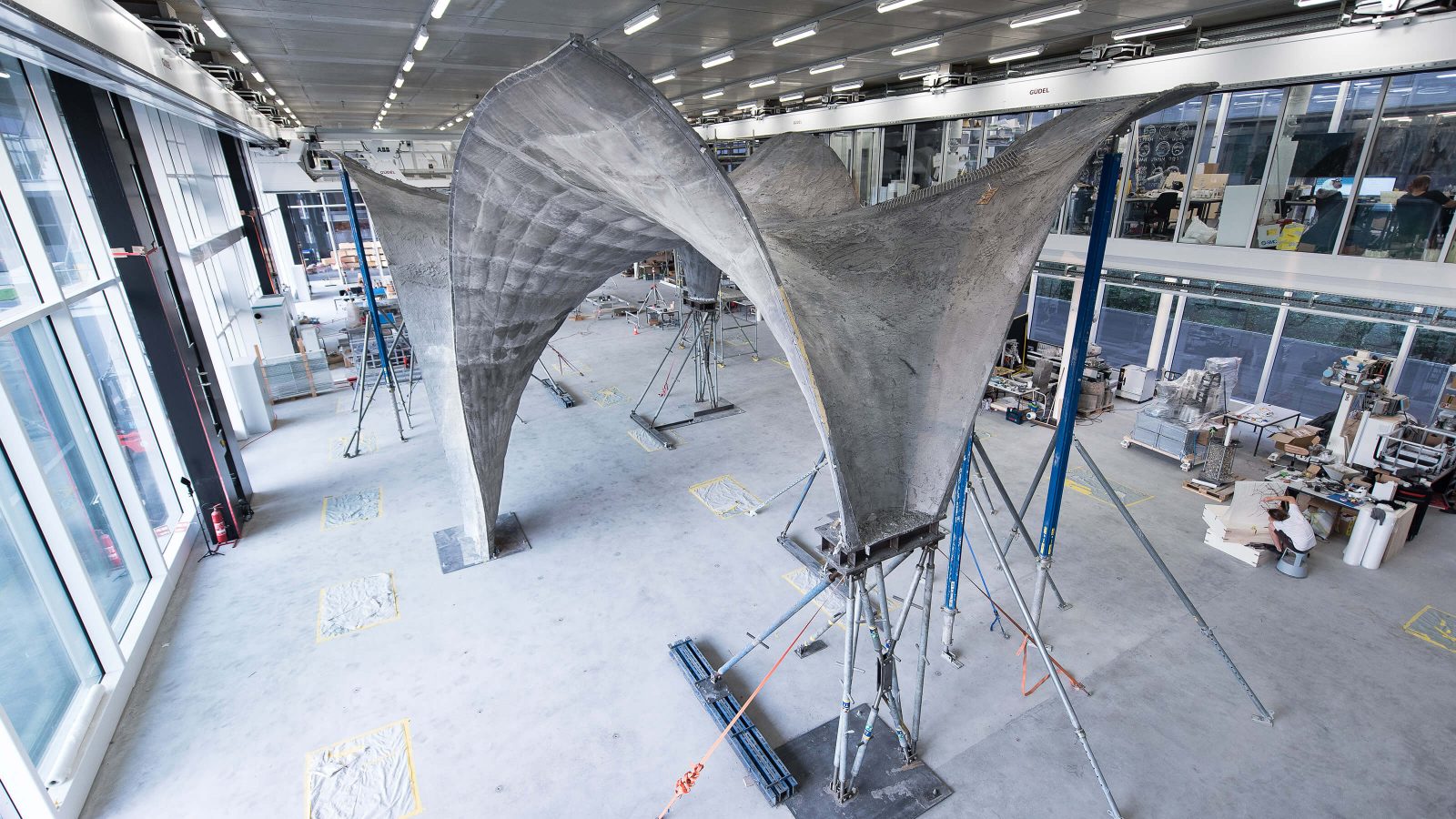
Last fall, ETH Zürich released a video that captured the making of an ultra-thin concrete roof, dubbed the HiLo. Catnip to architecture nerds, and having garnered some 300,000 online views just weeks after its release, it features builders working around a hatch-work scaffold base and a wooden edge-beam structure as they install a massive net of steel cables held taut by metal nodes.
These custom nodes are key to what makes HiLo an evolutionary, if not revolutionary, achievement. An algorithm in the roof’s computational model allows the designers to move the nodes and re-tension the cables, ensuring the forces are properly distributed among them, and that the form, deflected under the weight of wet concrete, hits the required shape exactly. A polymer fabric is then stretched across the cable net and lined with a mesh textile, which is then sprayed with concrete.
Once the 120-square-metre formwork (including the cable net, fabric and mesh) is peeled away, it reveals a canopy in the shape of a massive billowing blanket. While the time-lapse video runs less than two minutes, the HiLo prototype took six months to build and entailed six years’ worth of development research. Its realization offers a glimpse of the future of sustainable concrete construction.
“I’m excited about the times we’re living in,” says project co-director Philippe Block. “Digital fabrication is getting to a point where we can build complex geometries that aren’t limited by scaffolding and forming systems.”
As the namesake and founder of the Block Research Group at ETH Zürich, Block is as close to being a rock star as the field of architectural research allows. He has collaborated with Foster + Partners (on the Droneport project for Rwanda) and with Zaha Hadid Architects (Shajay Bhooshan, a ZHA associate, is doing his PhD in 3D printed concrete at Block Research Group). Seven years ago, Empa (Swiss Federal Laboratories for Materials Science and Technology) invited Block to propose a concept for a building in Dübendorf, Switzerland, that would be used as a laboratory to test energy-efficient architectural prototypes in the real world.
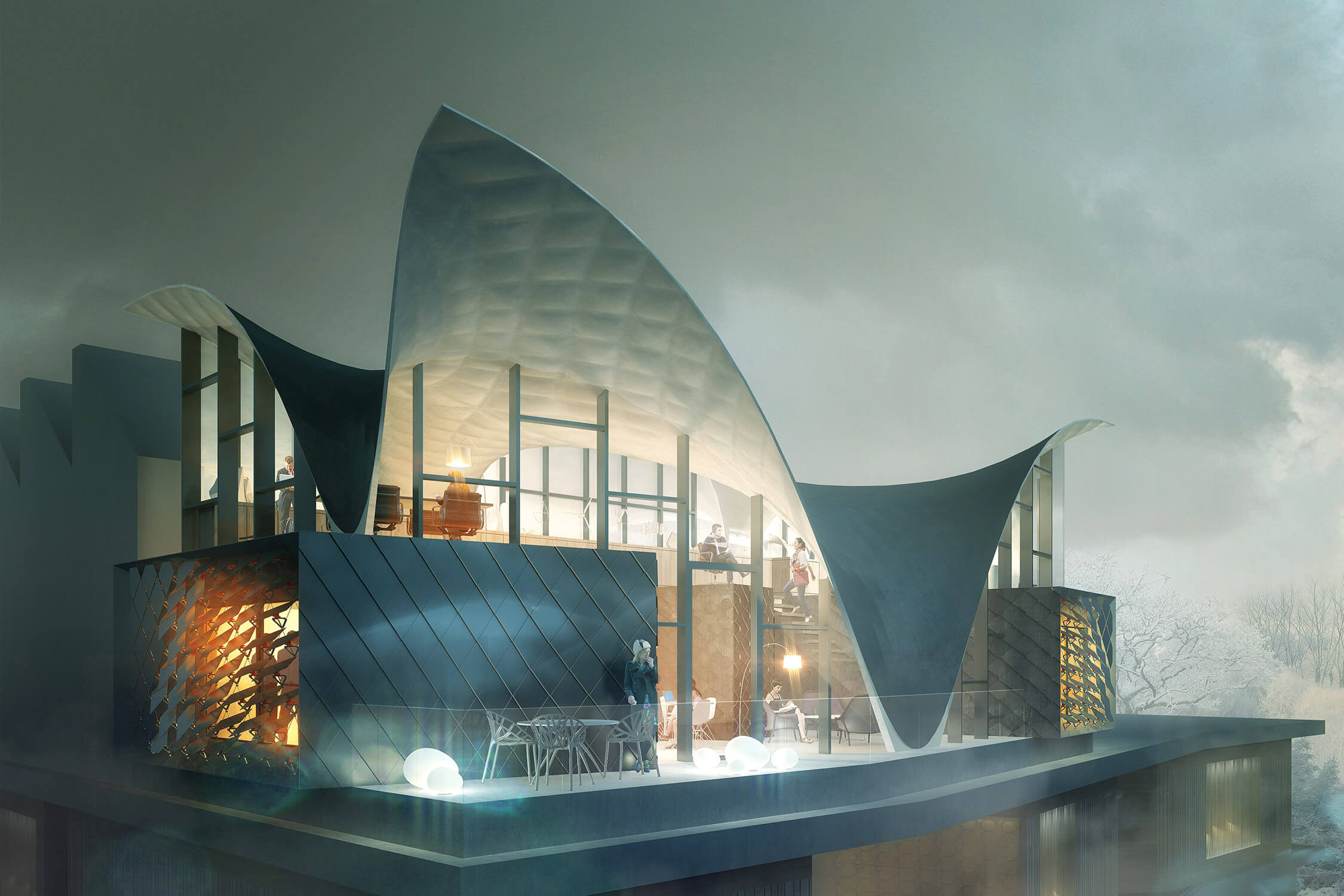
The HiLo roof is just one component of that project, called NEST, short for Next Evolution in Sustainable Building Technologies. The full HiLo structure is a two-storey penthouse that will top the building this spring, providing researchers with workspaces beneath a fluidly sculpted concrete shell. Other components of the building include a funicular vaulted floor system (more on this later) and a glazed facade punctured by boxy volumes sporting 200 individually controllable soft P.V. panels that will help the penthouse produce one-and-a-half times the energy it consumes.
To get his roof to this level of performance, Block turned to his ETH Zürich colleague Arno Schlüter, who then devised the heating and cooling coil system embedded into the concrete floors and roof, transforming these vast surfaces into gigantic radiators. To tie everything together, Block brought in Australian architecture firm Supermanoeuvre.
“The primary desire was to realize a more energy-efficient structure – and one that’s also more beautiful,” says Supermanoeuvre’s Dave Pigram. “Instead of sustainability being a burden that makes [a building] less interesting, when you do it precisely, you can make something that is exciting and unique.”
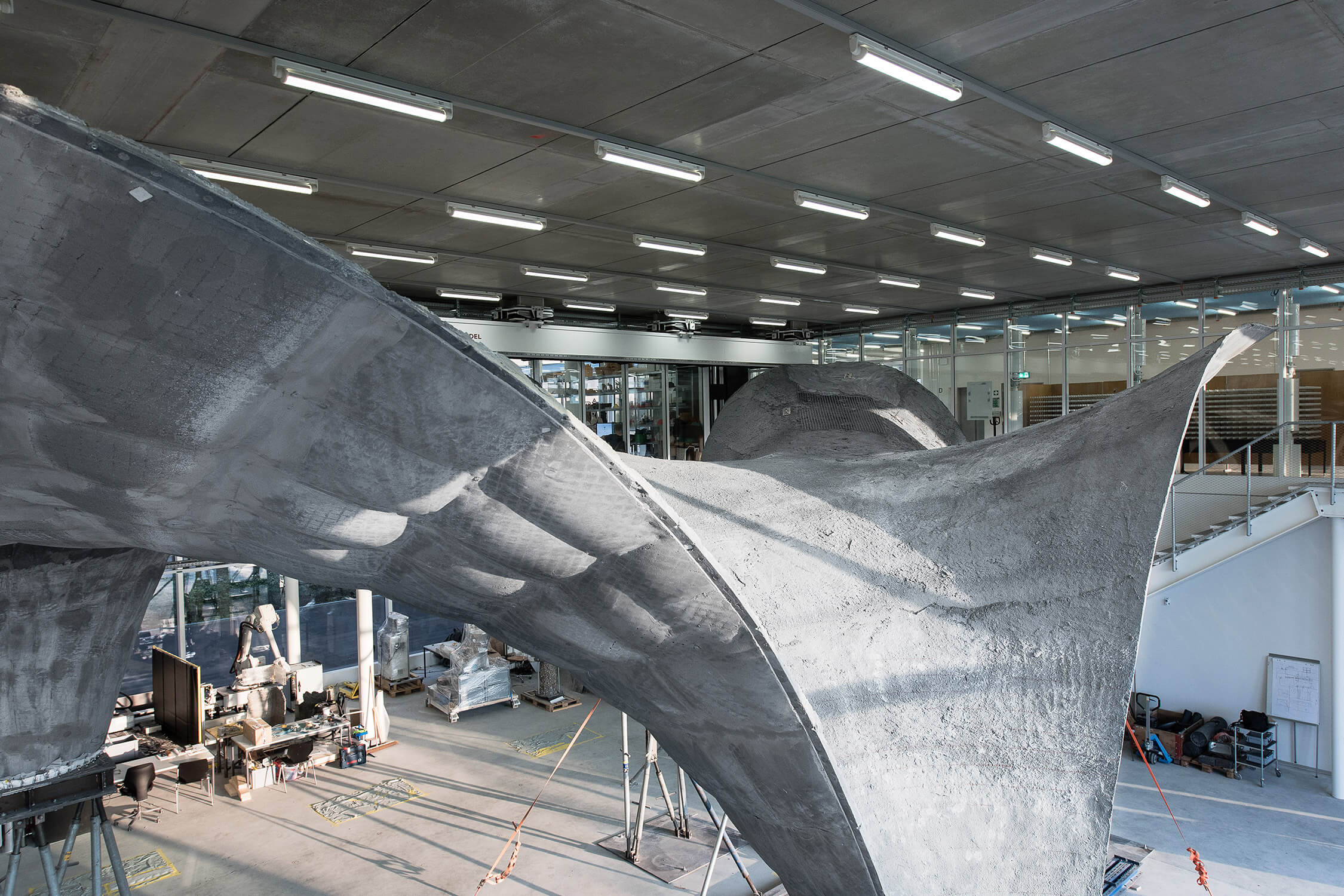
HiLo is among the most ambitious projects to demonstrate how concrete can be transformed into a sustainable material. The second-most prevalently used substance in the world (after water), concrete is made from cement – the manufacturing of which is responsible for five per cent of the world’s carbon dioxide emissions. It is also non-renewable and largely unrecyclable. The milled wood or foam formwork required to cast concrete is almost never recycled. What’s more, rebar plays a big role in concrete’s massiveness: In a mid- to high-rise tower, reinforced concrete accounts for 75 per cent of the building’s weight; of that bulk, floor slabs make up 90 per cent.
The truly exciting part of HiLo, then, is its funicular floor. Rather than take the shape of a massive, rebar-reinforced plate, it gains its structural integrity from its geometrically complex structure: a five-by-five-metre span of two-centimetre-thick ribs. Just as the ultra-thin roof does away with bulky formwork in favour of a fully recyclable cable-net and fabric hybrid weighing only 800-kilograms – which supported an impressive 20 tonnes of concrete – the innovative floor system requires just 30 per cent of a typical concrete slab floor.
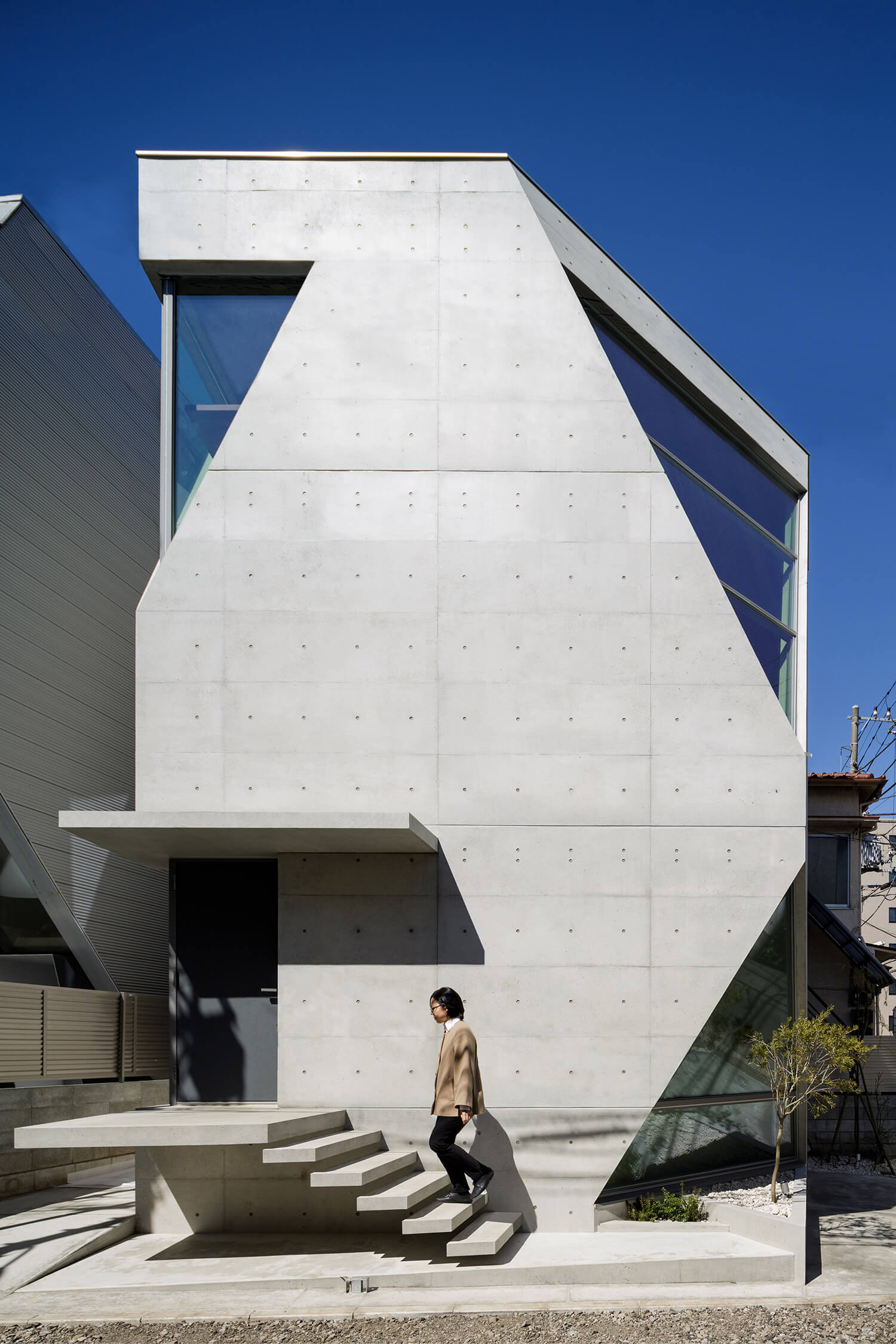
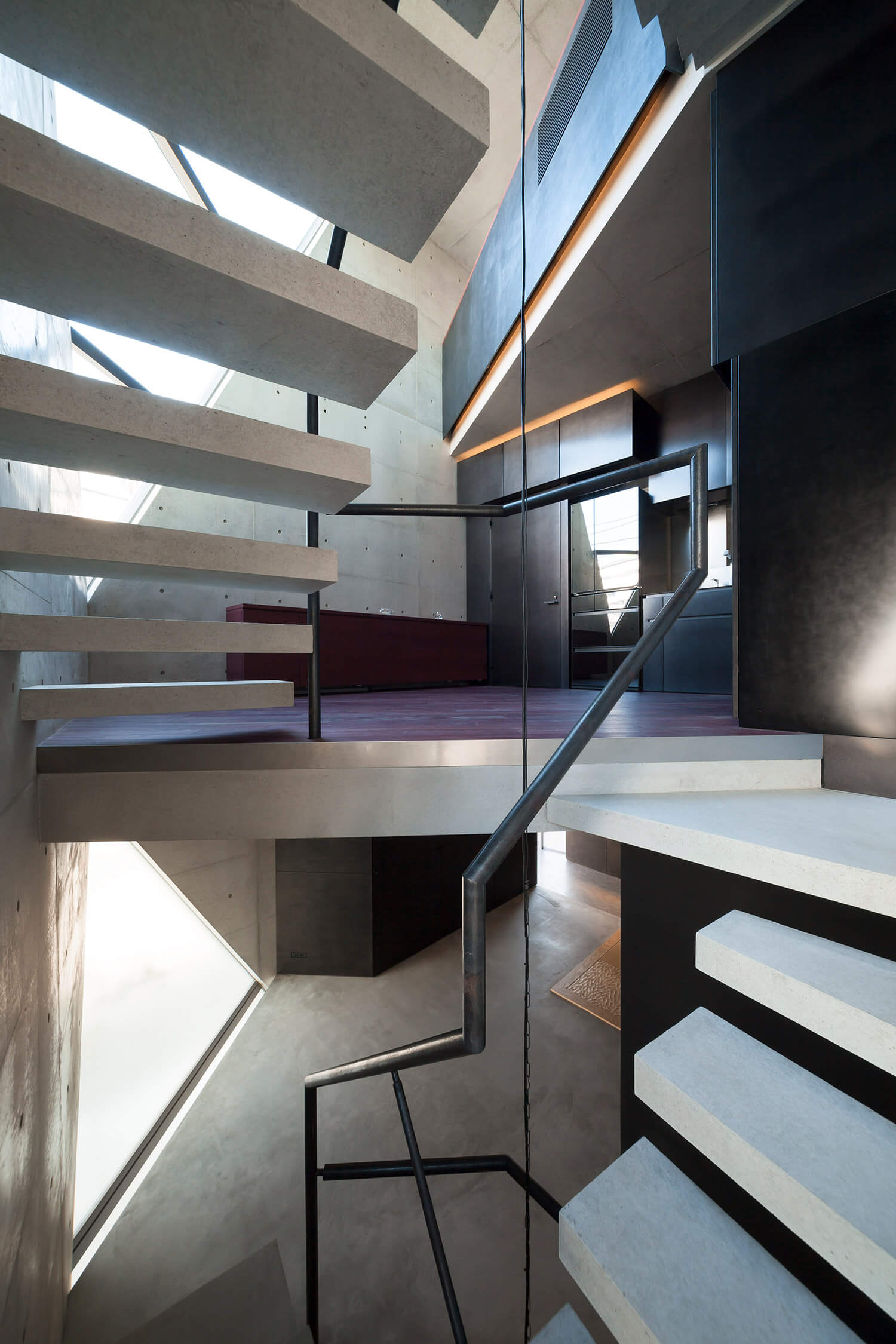
Concrete holds the architectural imagination like no other material. One need only point to the ongoing fascination with brutalism, which is fetishized all over Instagram and defended against the wrecking ball on #SOSBrutalism – a web database of more than 1,000 exposed-concrete buildings and an accompanying physical exhibition (on view at Deutsches Architekturmuseum in Frankfurt until April 2, 2018).
Toronto architect and educator Pina Petricone, who literally wrote the book on concrete, Concrete Ideas (2012), cites the material’s plasticity – “its amazing ability to depict an abstract space” – as its enduring appeal. But as breakthroughs in wood technologies are making inherently eco-friendly tall timber structures more viable, concrete needs to clean up its act. Petricone sees promising innovations.
“Making concrete sustainable is twofold,” she says. “It’s predicated on exploring how to recycle existing concrete, and secondly on developing at the molecular level types of concrete that you can use less of.”
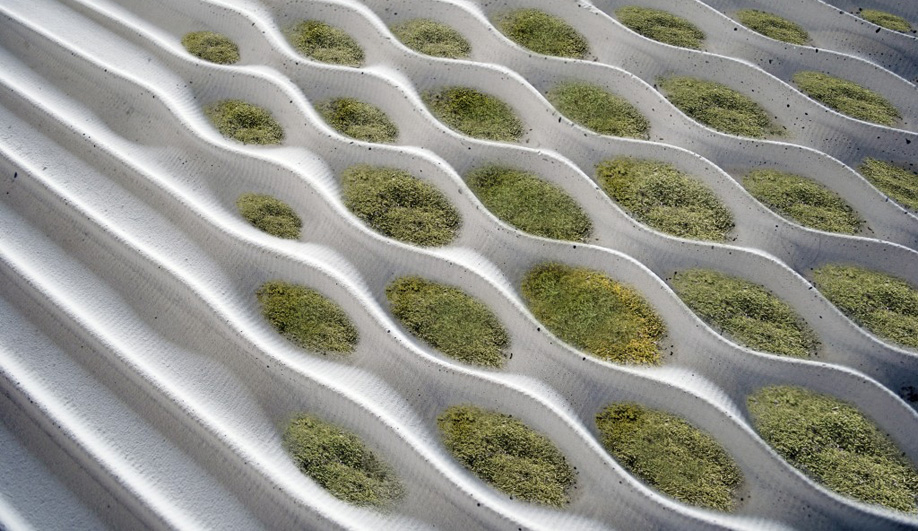
In fact, we’re in a boom cycle of innovation. While cement and concrete manufacturers such as Italcementi, Ductal and Lafarge are taking up the sustainability mantle – with cements that are smog-eating, ultra-thin, and ice repellent – some of the most radical ideas are emerging from academia and start-ups. These include doing away with wooden formwork by employing robotic arms to pump cement into custom fabric formwork, and eliminating moulds by 3D printing. Others are devising recipes for the admixture itself – can we make concrete, the material itself, green?
While participating in New York’s Biofabricate conference, Marcos Cruz takes a break to talk to me about the work he’s doing as a director of BiotA Lab at The Bartlett School of Architecture, which prototypes concrete that can sustain plant growth.
“We need to build differently to respond to and resist climate change. The forefront is biotechnology and synthetic biology,” Cruz proclaims. His team is experimenting with using magnesium phosphate to introduce porosity into concrete. As the concrete carbonates over time, it attains a surface roughness that allows it to absorb water. All of this is in service of attracting moss and lichen spores, which scrub the air of carbon dioxide and other pollutants.
Cruz and his team want to change the built environment completely, transforming passive exterior walls and infrastructure into “active agents” teeming with vibrant biological growth. BiotA Lab will get its first chance to gain traction for this wild idea with two real-world projects: a couple of sound-attenuating, bioreceptive retaining walls for Transport for London, and a mossy wall at a South London elementary school that kids can monitor and interact with.
MIT is also exploring how to remix concrete. Last year, the school’s nuclear science and civil engineering departments announced a breakthrough: an eco-concrete that is made stronger by adding recycled irradiated plastic. They knew that incorporating plastic usually weakens concrete; what they discovered was that by irradiating the plastic and combining it with fly ash, they could make the concrete tougher.
A provisional patent has been filed for the discovery, and though it will take years to get the new concrete to market, its potential to reroute huge mounds of plastic from the landfill is heartening. “A lot of people stand to benefit if this works out,” says MIT’s Michael Short.
Recycling is at the heart of another project aimed at lessening concrete’s environmental burden. Matter Design looks at past precedents to determine how concrete block itself can be recycled from old, crumbling structures. “Almost every culture in the past has done this,” says MD’s Brandon Clifford, “except for us.” Taking inspiration from the cyclopean stone walls built by ancient masons, the Boston-based firm has put together something called The Cannibal’s Cookbook – a digitized archive of architectural cannibalism, or architecture that reuses derelict buildings. The studio also built a mock wall – a bulging tapestry of boulders of varying size, shape and aggregate makeup – for the Seoul Biennale of Architecture and Urbanism.
If its concrete cannibalism makes Matter Design sound druidic, the firm is in fact cutting-edge, experimenting with concrete in ways that are resolutely modern. For instance, its Microtherme installation, which plays with lightness and heft, creates the illusion of a solid concrete doughnut floating inside a wood-clad cube. But the doughnut is, in fact, an incredibly thin shell made of glass-fibre reinforced concrete and EPS foam. “If someone is standing in it,” says Clifford, “it appears that the human body is pulling the concrete up and down – that the human body is massive rather than the concrete.” The project was shortlisted for an AZ Award last year.
Whatever shape concrete takes, the formwork needs to be reimagined, and some solutions are beginning to make their way into practice. In March 2017, for Amazon’s MARS conference in Palm Springs, the Los Angeles studio Form Found Design created a catenary dome that used robotic arms to create 70 concrete forms. The installation was erected in three days, with each piece bolted together within 1/16th of an inch, “to the delight of Jeff Bezos,” says Form Found Design’s Joseph Sarafian. He adds: “We can now create these Gaudí-like catenary curves with digital tools.”
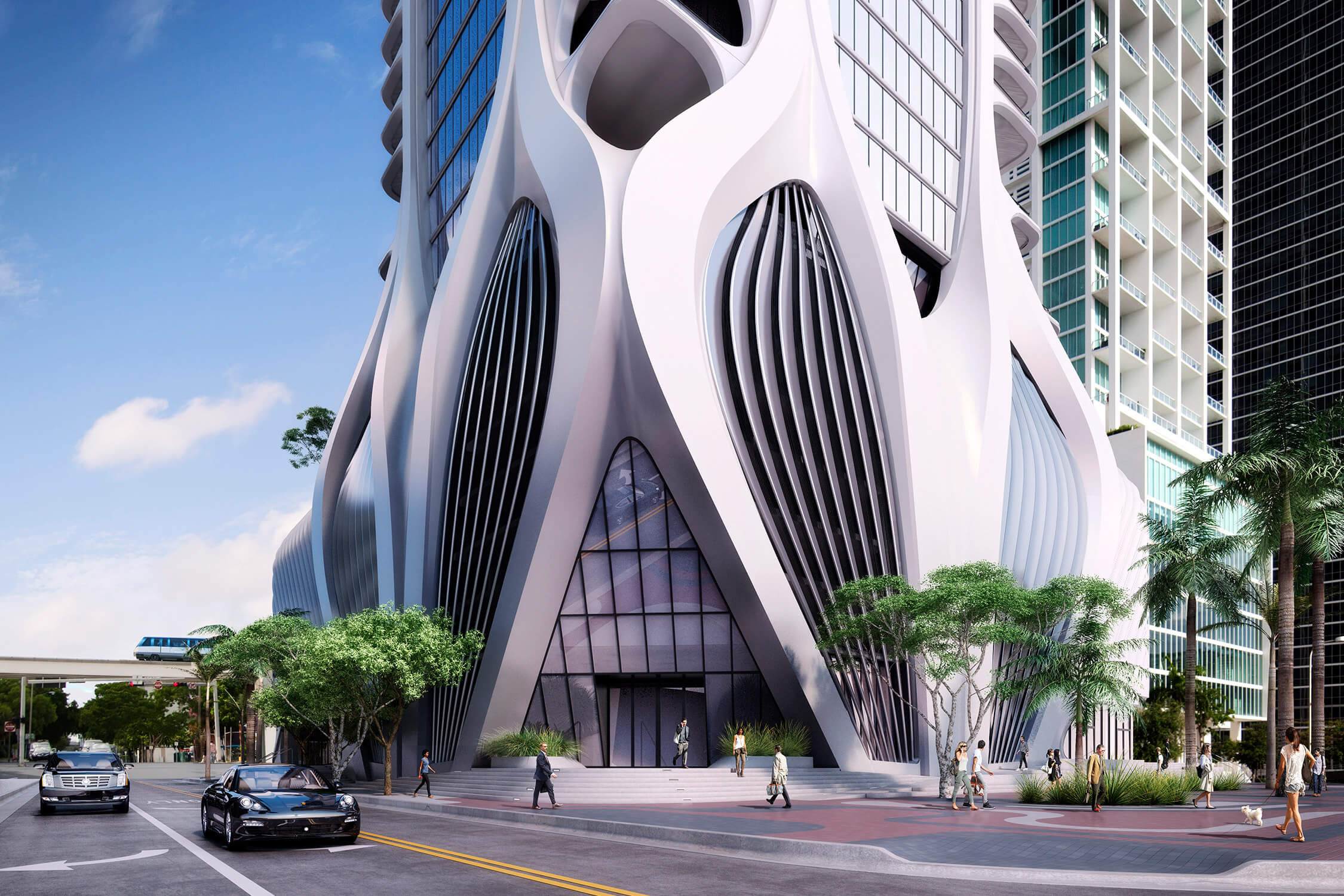
Another sustainable way of building complex concrete architecture is with 3D printing. Although the technology may still seem nascent, one of the world’s most renowned firms has fully embraced it. ZHA’s buildings form a taxonomy of concrete firsts: MAXXI boasted the world’s largest single pour of concrete (22.9 metres tall); the Phaeno Science Center’s complex shape spurred the development of new concrete mixes; and the Heydar Aliyev Center combined glass-fibre reinforced concrete and polyester with a novel space-frame system. “Concrete printing has been 20 years in gestation, and only now is it catching fire,” says Shajay Bhooshan of ZHA. “In the next two to three years,” he predicts, “there will be significant activities.”
Just as his HiLo project is capturing the world’s imagination, Block, like Bhooshan, sees 3D printing as one of the next frontiers for both the form and aesthetic of concrete. Block wants to maximize the technology’s potential to create complex geometric and aesthetic forms at the scale of a building. “We are developing a language of forms that is more in line with 3D printing; forms that are ‘custom-tailorizable’ – though that’s definitely not a word, it is the holy grail.”
Block’s enthusiasm is warranted – he and his contemporaries are clearly on to something. To build sustainably and create something “beautiful,” to use Dave Pigram’s word: That will be the driving force for concrete innovation from here on out.
One of the world’s most polluting building materials is undergoing a seismic revolution, becoming a leaner, lighter and smarter version of itself.